Roads from plastic waste
S.S. Verma
The debate on the use and abuse of plastics vis-a-vis environmental protection can go on, without yielding results until practical steps are initiated at the grassroots
level by everyone who is in a position to do something about it. The plastic wastes could be used in road construction and the field tests withstood the stress and proved that plastic wastes used after proper processing as an additive would enhance the life of the roads and also solve environmental problems. The present write-up highlights the developments in using plastics waste to make plastic roads.Plastic is everywhere in today’s lifestyle. It is used for packaging, protecting, serving, and even disposing of all kinds of consumer goods. With the industrial revolution, mass production of goods started and plastic seemed to be a cheaper and effective raw material. Today, every vital sector of the economy starting from agriculture to packaging, automobile, building construction, communication or infotech has been virtually revolutionised by the applications of plastics. Use of this non-biodegradable (according to recent studies, plastics can stay unchanged for as long as 4500 years on earth) product is growing rapidly and the problem is what to do with plastic-waste. Studies have linked the improper disposal of plastic to problems as distant as breast cancer, reproductive problems in humans and animals, genital abnormalities and even a decline in human sperm count and quality. If a ban is
put on the use of plastics on emotional grounds, the real cost would be much higher, the inconvenience much more, the chances of damage or contamination much greater. The risks to the family health and safety would increase and, above all the environmental burden would be manifold. Hence the question is not ‘plastics vs no plastics’ but it is more concerned with the judicious use and re-use of plastic-waste. Plastics roads Plastic use in road construction is not new. It is already in use as PVC or HDPE pipe mat crossings built by cabling together PVC (polyvinyl chloride) or HDPE (high-density poly-ethylene) pipes to form plastic mats. The plastic roads include transition mats to ease the passage of tyres up to and down from the crossing. Both options help protect wetland haul roads from rutting by distributing the load across the surface. But the use of plastic-waste has been a concern for scientists and engineers for a quite long time. Recent studies in this direction have shown some hope in terms of using plastic-waste in road construction i.e., Plastic roads. A Bangalore-based firm and a team of engineers from R. V. College of Engineering, Bangalore, have developed a way of using plastic waste for road construction. An initial study was conducted in 1997 by the team to test for strength and durability. Plastic roads mainly use plastic carry-bags, disposable cups and PET bottles that are collected from garbage dumps as an important ingredient of the construction material. When mixed
with hot bitumen, plastics melt to form an oily coat over the aggregate and the mixture is laid on the road surface like a normal tar road. Basic process Waste plastic is ground and made into powder; 3 to 4 % plastic is mixed with the bitumen. Plastic increases the melting point of the bitumen and makes the road retain its flexibility during winters resulting in its long life. Use of shredded plastic waste acts as a strong “binding agent” for tar making the asphalt last long. By mixing plastic with bitumen the ability of the bitumen to withstand high temperature increases. The plastic waste is melted and mixed with bitumen in a particular ratio. Normally, blending takes place when temperature reaches 45.5°C but when plastic is mixed, it remains stable even at 55°C. The vigorous tests at the laboratory level proved that the bituminous concrete mixes prepared using the treated bitumen binder fulfilled all the specified
Marshall mix design criteria for surface course of road pavement. There was a substantial increase in Marshall Stability value of the BC mix, of the order of two to three times higher value in comparison with the untreated or ordinary bitumen. Another important observation was that the bituminous mixes prepared using the treated binder could withstand adverse soaking conditions under water for longer duration. The durability of the roads laid out with shredded plastic waste is much more compared with roads with asphalt with the ordinary mix. Roads laid with plastic waste mix are found to be better than the conventional ones. The binding property of plastic makes the road last longer besides giving added strength to withstand more loads. While a normal 'highway quality' road lasts four to five years it is claimed that plastic-bitumen roads can last up to 10 years. Rainwater will not seep through because of the plastic in the tar. So, this technology will result in lesser road repairs. And as each km of road with an average width requires over two tonnes of polyblend, using plastic will help reduce non-biodegradable waste.
The cost of plastic road construction may be slightly higher compared to the conventional method. However, this should not deter the adoption of the technology as the benefits are much higher than the cost.
'''''''''''''''''''''''''''''''''''''''''''''''''''''''''''''''''''''''''''''''''''''''''''''''''''''''''''''''''''''''''''''''''''''''''''''''''''''''''''''''''''''''''''''''''''''''''''''''''''''''''''
K. Ahmed Khan is an Indian scientist and businessman who made success in using plastic for road construction.[1] He is the founder of KK Plastic Waste Management Pvt.Ltd.He along with his brother Rasool Khan,stung by protests to ban plastic, hit upon the idea of recycling plastic and mixing it with bitumen to lay roads. Thanks to their enterprising spirit, they have so far laid almost 1,000 km of roads — Lalbagh Road, Cunningham Road, Old Madras Road and many others — in the city with recycled plastic. RESEARCH & IMPLEMENT Rasool, the director of K K Plastic Waste Management Private Limited, tells Bangalore Mirror how the brothers came up with the idea of recycling plastic for roads: "In 1996, there were demands for a ban on plastic. Our entire livelihood depended on plastic as we manufacture plastic bags for our company called K K Polyflex. We also had about 100-odd employees working with us. So we thought of researching on alternate uses of plastic." During their research the Khans realised that plastic could be used along with bitumen to make roads. After reading up about Bangalore roads, they thought of laying such roads in the city. In 1996, Rasool (59) made the first trial use of plastic with bitumen. He successfully used the bitumen-plastic mixture to fill about 100-200 potholes on Rajalakshmi Nursing Home Road in Jayanagar. He then asked his son Amjad Khan, who was then studying chemical engineering at RV College of Engineering, to take this up as a research project and also funded it. After two years of research work, Amjad concluded that it was feasible to use bitumen-plastic in laying roads. Next, they needed the approval from experts in highway Engineering. Highway engineering professors Justo and Vir Raghavan from the Bangalore University took special interest in the idea and studied it. Now, they had to get the approval of Central Road Research Institute, Delhi. After a two-year they got the green signal from CRRI. Armed with approvals from all quarters, the brothers met the then Karnataka CM S M Krishna. Thanks to the CM's encouragement, the Khans laid their first plastic waste road in front of Rajarajeshwarinagar front gate in 2002. In the first year of their road work, they were paid Rs 11 lakh by the government. "In 2003-04 we signed a Memorandum of Understanding with the BBMP to lay 250 km of roads," says Rasool. Some of the roads they have laid include Millers Road, Cunningham Road, Old Madras Road, J C Road, Lalbagh Road, almost all roads in Jayanagar, and Mysore Road till Kanakpura Junction. FROM WASTE TO ROAD The company gets approximately five tons of plastic waste every day. It buys plastic waste at Rs 6 per kg from apartments, schools, ITC factory, and pourakarmikas. Rasool says, "We also have our own auto and lorry that picks up plastic waste strewn around the city." The plastic waste thus collected is cleaned and put in a shredder. The shredded bits are then stored in bags for six to seven days to drain out the moisture in them. The shredded plastic is then taken to a hot mixing plant located on the city outskirts, where it is mixed with bitumen to make roads. The bitumen-plastic mix is called K K Poly Blend. Ahmed Khan (61), an alumni of St Joseph's College of Commerce, says, "Normally the life of a road is about three years. But with K K Poly Blend it increases to about six to seven years. This is because the melting point of bitumen is about 60 to 70 degrees where as plastic's melting point is about 130 to 140 degrees. Moreover, Bangalore generates 5,000 tonnes of solid waste every day, out of which at least 50 tonnes is plastic. If all that plastic waste is used the remaining solid waste can be used to make organic manure." He reasons, "Every day India produces 1,23,000 tonnes of waste, out of which about 2000 tonnes is plastic. If we can use all that plastic, the plastic waste problem can be solved." Their plastic road concept has even attracted attention from the Burmese government and entities in Italy.
''''''''''''''''''''''''''''''''''''''''''''''''''''''''''''''''''''''''''''''''''''''''''''''''''''''''''''''''''''''''''''''''''''''''''''''''''''''''''''''''''''''''''''''''''''''''''''''''''''
Utilisation of Waste Plastic Bags in Bituminous Mix for Improved Performance of Roads.
Centre for Transportation Engineering, Bangalore University, Bangalore, India
Prof. C.E.G. Justo Honorary Professor, Bangalore University Bangalore and Dr. A. Veeraragavan Co-ordinator, Centre for Transportation Engineering, Bangalore University, Bangalore - 560 0056.
1. INTRODUCTION;
The use of thin plastic bags to pack and to carry various materials including house hold articles has become a common practice all over the country. However the disposal of the waste plastic bags in large quantities has been a problem and is of great concern, particularly in big cities. The mixing up of these waste plastic bags with other bio-degradable organic waste materials in the garbage of the urban areas has been the main cause of the problem. Therefore attempts are being made in some cities to limit or even to prohibit the use of the thin plastic bags for packing and other common use, so as to control this "undesirable waste material" from getting mixed up with the other organic garbage.
In case it is possible to find useful application for the waste plastic bags, there will be substantial scrap value for this waste product and therefore they will be collected and sold by interested persons, instead of being littered or thrown out in the dust bins or into the road side drains.
At the initiative of M/s K.K. Poly Flex Pvt. Ltd., a study on the possible use of the processed plastic waste bags with the bituminous mixes was carried out at the R.V. College of Engineering Bangalore. A group of students of B.E. degree course in Chemical Engineering of this college under the guidance of the concerned teaching staff carried out their final year project work for studying the possibility of using of the processed plastic bags with bitumen and bituminous mixes(2). As some encouraging results were reported in this study, M/s K.K. Poly Flex Pvt. Ltd. later approached the Centre for Transportation Engineering of Bangalore University with the request to carry out further research studies on the effects of using the processed plastic bags with bituminous mixes for road construction works. This company supplied the processed plastic material and they also helped the Centre for developing some additional facility to test the bituminous mix specimens under controlled temperature.
2. USE OF RE-CYCLED PLASTICS AS ADDITIVES IN BITUMINOUS MIXES
It has been possible to improve the performance of bituminous mixes used in the surfacing course of road pavements, with the help of various types of additives to bitumen such as polymers, rubber latex, crumb rubber- treated with some chemicals, etc. Some limited studies have been reported on the use of re-cycled plastic, mainly polyethylene, in the manufacture of polymer - modified asphalt cement or bitumen. According to Larry Flynn (3), re-cycled polyethylene from grocery bags may be useful in asphaltic (bituminous) pavements, resulting in reduced permanent deformation in the form of rutting and reduced low - temperature cracking of the pavement surfacing.
Salah E. Zoorob (4) and Zoorob and Suparma (5) have shown that re-cycled plastics composed predominantly of polypropylene and Low Density Polyethylene can be incorporated into conventional asphaltic (bituminous) road surfacing mixtures. Greater durability and fatigue life have been reported in these modified mixes as compared to conventional mixes.
3. RECENT STUDIES ON THE USE OF PROCESSED PLASTIC BAGS IN BITUMINOUS CONCRETE MIXES
3.1 General Findings
Laboratory studies were carried out at the Centre for Transportation Engineering of Bangalore University on the possible use of the processed plastic bags as an additive in bituminous concrete mixes(6). The material used in this study was supplied by M/s KK Poly Flex (P) Ltd., Bangalore. The processed plastic was used as an additive with heated bitumen in different proportions ( ranging from zero to 12 % by weight of bitumen) and mixed well by hand, to obtain the modified bitumen.
The properties of the modified bitumen were compared with ordinary bitumen. It was observed that the penetration and ductility values of the modified bitumen decreased with the increase in proportion of the plastic additive, up to 12 % by weight. The softening point of the modified bitumen increased with the addition of plastic additive, up to 8.0 % by weight.
Studies were carried out on Bituminous Concrete (BC) mixes using 80 / 100 grade bitumen having average Marshall Stability Value (MSV) of 1100 kg at optimum bitumen content of 5.0 % by weight of the mix. Further studies on BC mixes were carried out using the modified binder obtained by the addition of varying proportions of processed plastic bags (percentage by weight of bitumen) with the conventional 80 /100 grade bitumen. The optimum modified binder content fulfilling the Marshall mix design criteria was found to be 5.0 % by weight of the mix, consisting of 8.0 % by weight of processed plastic added to the bitumen. The average MSV of the BC mix using the modified binder was found to be as high as 3312 kg at this optimum binder content, resulting in about three fold increase in stability of the BC mix, which contains 4.6 % bitumen plus 8 % processed plastic by weight of bitumen, i.e., 0.4 % processed plastic by weight of the mix.
In order to evaluate the ability of the BC mix prepared with the above-modified bitumen to withstand adverse soaking condition under water, Marshall stability tests were conducted after soaking in water at 60 Co for 24 hours. The average MSV of the BC mix with modified binder (using 8 % processed plastic by weight of bitumen, as above) was found to increase by about 2.6 times of the mix with ordinary bitumen. Further laboratory studies carried out on the BC mixes using this modified binder also indicated note worthy increase in fatigue life under repeated application of loads.
Thus the laboratory investigations carried out so far at Bangalore University have given highly encouraging results for the use of bituminous concrete mixes in the surfacing course of road pavements by using this modified binder which is prepared by the addition of 8.0 % of the processed plastic, by weight of bitumen. 3.2. Advantages of Using Modified Bitumen with Processed Plastic as Additive
i) The use of modified bitumen with the addition of processed plastic, about 8.0 % by weight of bitumen, helps in substantially improving the stability or strength, fatigue life and other desirable properties of bituminous concrete mix, even under adverse water-logging conditions. Therefore the life of the pavement surfacing course using the modified bitumen is also expected to increase substantially in comparison to the use of ordinary bitumen.
ii) The addition of 8.0 % by weight of processed plastic for the preparation of modified bitumen results in a saving of 0.4 % bitumen by weight of the mix or about 9.6 kg bitumen per cubic metre (m 3) of BC mix. This results in a saving of about Rs.110 per m 3 of BC mix based on the present cost of 80 / 100 grade bitumen, ( as of June, 2001 ).
iii) The effective utilisation of the waste plastic bags for the preparation of modified bitumen will result in substantial increase in the scrap value for this other wise "undesirable waste material", which are getting littered all over the urban areas. These waste plastic bags will not therefore be thrown out along with the garbage; instead they will get collected and sold by the consumers themselves or other agencies, due to the attractive scrap value.
4. NEED FOR FURTHER WORK
It is necessary to work out a project proposal to carry out further studies on various aspects such as collection, processing and effective utilisation of this waste material. To start with, such a study could be initiated in Bangalore, with the following components :
i) Estimation of the types, quantity and useful components present in the waste plastic materials in the city and surrounding areas
ii) Methodology for collection and sorting out the useful components of the plastic waste
iii) Methodology for processing the plastic bags as required for use in the preparation of modified bitumen, including cleaning, shredding and further processing of the plastic waste materials
iv) Identification of two or three construction companies / entrepreneurs who could incorporate appropriate mixing units in their bitumen boiler / hot mix plant to add and mix the required proportion of the processed plastic additive
v) Carrying out further laboratory investigations, construction of some test tracks and field studies on the performance of pavements using the modified bitumen
vi) Working out relative economics of using the modified bituminous mixes in road construction works, considering the improved performance and increased service life of the pavement
vii) Preparation of specifications and standards for the construction industry.
It is hoped that on completion of the above project, the plastic waste materials will be put to effective use in road construction industry, resulting in improved road pavements and also relief from the waste plastic materials being littered all around urban areas.
5. SOME SELECTED REFERENCES
1. Robin L Schroeder, "The Use of Recycled Materials in Highway Construction", Journal, Public Roads, Vol. 58, No. 2 (1994 )
2. Amjad Khan, Gangadhar, Murali Mohan and Vinay Raykar, "Effective Utilisation of Waste Plastics in Asphalting of Roads". Project Report prepared under the guidance of R. Suresh and H. Kumar, Dept. of Chemical Engg., R.V. College of Engineering, Bangalore, 1999.
3. Larry Flynn, "Recycled Plastic Finds Home in Asphalt Binder", Journal, Roads and Bridges, March 1993
4. Zoorob S.E. and Suparma, L.B., "Laboratory Design and Investigation of Proportion of Bituminous Composite Containing Waste Recycled Plastics Aggregate Replacement (Plastiphalt), CIB Symposiumon Construction and Environment Theory into Practice, Sao Paulo, Brazil ( November, 2000 )
5. Zoorob, S.E., "Laboratory Design and Performance of Improved Bituminous Composites Utilising Plastics Packaging Waste", Conference on Technology Watch and Innovation in Construction Industry, Belgium, Building Research Institute, Brussels, Belgium (April, 2000)
6. Research Work at the Centre for Transportation Engineering, Bangalore University during the year 2000 - 2001 and the Seminar Report on "Study of the Effect of Plastic Modifier on Bituminous Mix Properties" by V.S. Punith, II Semester, M.E. (Civil) Highway Engg., Dept. of Civil Engineering, Bangalore University (March, 2001).
""""""""""""""""""""""""""""""""""""""""""""""""""""""""""""""""""""""""""""""""""""""""""""""""""""""
Use of Plastic Wastes in the Construction of Roads
Written by Dr. Yashpal Singh
Bitumen is a useful binder for road construction and elastomers like natural rubber, crumb rubber, SBR, etc. as well as plastomeric substances like Polyethylene, Ethylene Vinyl Acetate and Ethylene Butyl Acrylates are mixed with bitumen to modify its properties to give better quality. By adding small amounts of polymers to bitumen, the life span of the road pavement may be considerably increased.
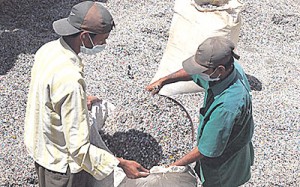
Thinner polythene/polypropylene carry bags are the most abundantly disposed of wastes, which may not be collected by ragpickers for onward recycling because of lower returns. These polythene/polypropylene bags are easily compatible with bitumen at specified conditions and a blend can be prepared and used for road laying.
Almost 90% of the polymeric materials are made up of either polyethylene or polypropylene or polystyrene, which being heated at around 130-1400c gets softened without releasing any gaseous products, while, when PVC is incinerated (>7000c), it may produce toxic gases like Dioxins.
Homopolymers, like high and low density polyethylene and polypropylene, as well as random and block copolymers, like ethylene-vinyl acetate, ethylene/propylene, styrene-b-butadiene-b-styrene and styrene-b-ethyl-ene-co butylene-b-styrene, have been used as bitumen modifiers. Polymer blended bitumen has better properties regarding softening point, penetration point, ductility, stripping value and marshall stability value. Hence the blend can be used for laying flexible pavement.
In the process of the preparation of polymer-bitumen aggregate mix, the temperature used is only-1700C and no chlorine or copper is present in the system. The polymer materials used are polyethylene, polypropylene and polystyrene only and polyvinyl chloride is not used to avoid the possibility of presence of chlorine in the system because of which Dioxin does not form.
The whole process is very simple and economical and needs no new machinery.
The technology is also very simple and the waste plastics available in the surrounding area can be used then and there.
Crumb rubber requires a temperature of 1800C whereas 60/70 grade bitumen needs 1600C only. This accounts for fuel conservation.
Roads have been laid at different places at Tamil Nadu using different surface area and different composition are performing well.
A scheme for laying waste plastics-Tar road in rural area for 1000 km was launched on 16th July, 2003 at Namakkal by the Honourable Chief Minister of Tamil Nadu Dr. J. Jayalalitha.
No comments:
Post a Comment